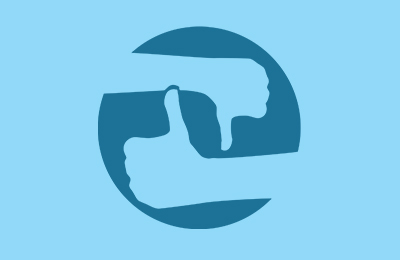
The Pros and Cons of Closed Cell Foam Insulation
If you’re considering spray foam insulation for your home, and aren’t sure whether it’s the right choice, it is important to consider what is most important to you. The best choice for your insulation project boils down to deciding whether it is more important to save some money now, or save far more in the long run.
Making your choice becomes easier when you consider the pros and cons of closed cell spray foam insulation. The focus of this post is closed cell spray foam as opposed to open cell foam because it is the most energy efficient and most commonly used type.
Cons
Spray foam is impractical as a DIY project
- Installation of spray foam insulation requires expensive, specialized, and difficult to use spray equipment and processes.
- The installation process can also be messier than installing other insulations. Avoiding unwanted mess can be complicated if you’re unsure how to protect the area that you’re working in and how to handle clean up once the job is done.
It’s worth nothing that no matter what material you choose, installing insulation in your home is not a matter to be taken lightly. Without adequate previous experience installing insulation, there is more room for error, injury, and poor results when important steps are inadvertently overlooked. As a general rule of thumb, installing insulation is best left to the certified professionals who are spray foam insulation experts.
More expensive upfront cost
- The cost of installing spray foam insulation is generally 2-3 times more expensive upfront than traditional fiberglass insulation.
This cost difference is mainly due to the need for professional installation, which many people opt for anyway even when choosing traditional fiberglass insulation. It’s also important to balance the installation cost with the fact that it only takes on average of 2-4 years before the benefit of energy bill savings outweighs the cost difference between spray foam insulation and cheaper insulation like fiberglass. Every year past that point is just money in your pocket. Looking into the future even further, you avoid the significant cost of needing to replace cheap insulation as early as 10 years down the line.
Pros
Spray foam is the most energy efficient insulator
- Because it expands, spray foam fills in gaps and holes other types of insulation can’t and creates an efficient, airtight seal.
- Spray foam’s insulation r value (resistance value) is 6.0-6.5, one of the highest values available on the market.
- Unlike other insulation materials, spray foam’s r value remains stable over time.
- These resistant properties result in a thermal envelope, causing more consistent in-home temperatures.
- Homes with spray foam insulation have lower HVAC system capacity requirements (meaning your air conditioner and furnace don’t have to work as hard to reach a comfortable temperature).
The net effect of all of these properties is that spray foam insulation is highly energy efficient, stays that way long-term, and results in significant energy bill savings.
Spray foam is not only airtight but is also water-tight
- Closed cell spray foam does not absorb water or moisture. Other insulation materials do!
- FEMA has classified spray foam as highly resistant to floodwater damage
- Even after flooding and/or exposure to water, spray foam insulation can be cleaned of most pollutants. This is not possible with most other materials.
- Mold and mildew cannot feed or thrive off of spray foam’s inert polymer composition, making it a mold deterrent
- Spray foam’s airtight properties reduce the infiltration of allergens like pollen and dust
Spray foam’s airtight, cleanable, mold resistant properties create healthier air quality when professionally installed in homes. If you have allergies or live in flood-prone areas, spray foam is an especially great way to improve your comfort, health, and peace of mind at home.
Indefinite lifespan
- Spray foam insulation, once installed, is structurally permanent and will not settle or break down.
- Unlike any other materials, spray foam actually adds structural strength to a building’s walls!
As we mentioned earlier, traditional materials like fiberglass settle and shift over time. To remain effective, fiberglass sometimes has to be completely re-done as soon as ten years after installation. Spray foam insulation doesn’t.
Looking deeper…
If these pros and cons have piqued your interest about spray foam insulation but you’d like to learn more, we have created a guide with more details and data. It’s completely free, and you can download “The Top 5 Benefits of Spray Foam Insulation” here.